Bridge Plug
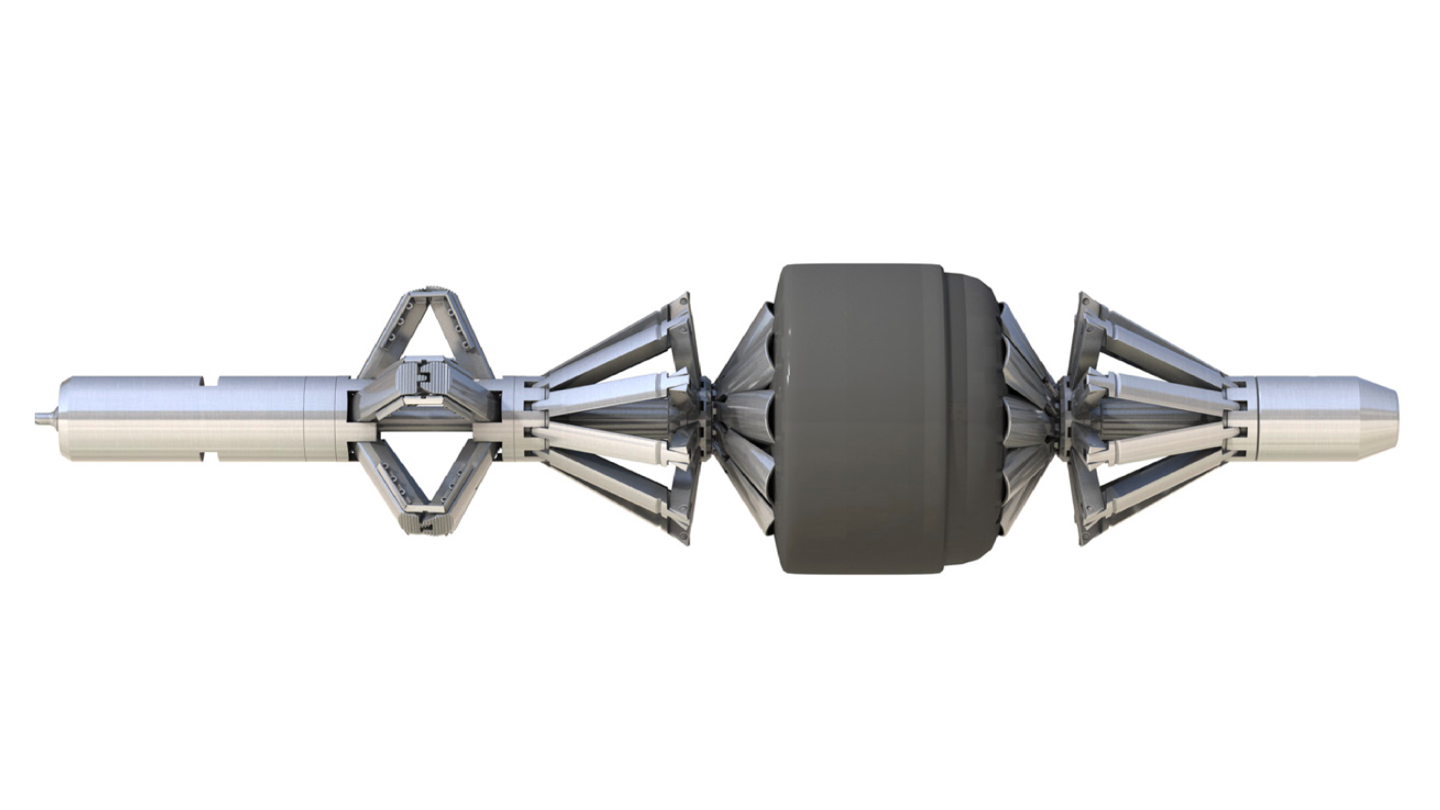
When designing a High-Expansion Thru-Tubing Bridge Plug (TTBP), Halliburton turned to us to provide specialized knowledge in the modelling and simulation of kinematics, non-linear mechanics and stress and strain analysis. In this case we augmented their team to produce the design you see above.
We focused on the design of the anchoring slips, centralizers and anti-extrusion petals – essentially all of the deployable elements. For each of these we generated and simulated a kinematic model to ensure that the deployment action was smooth and free from potential hang-ups. We also evaluated the stress and strain conditions of each component under the extreme loading expected in practice to ensure that the risk of structural failure was minimized. Finally, we evaluated potential upset scenarios such as the misalignment of the anchoring slips due to trapped debris to ensure robustness and reliability.
These actions enabled the identification of higher risk failure modes that were addressed through design changes before the first prototype was even built because these could be validated virtually at a fraction of the cost of testing. The benefit was reduced testing that was limited to the validation of the complete device.
Halliburton currently markets this award-winning design.